A Akrapovič por dentro – Parte II
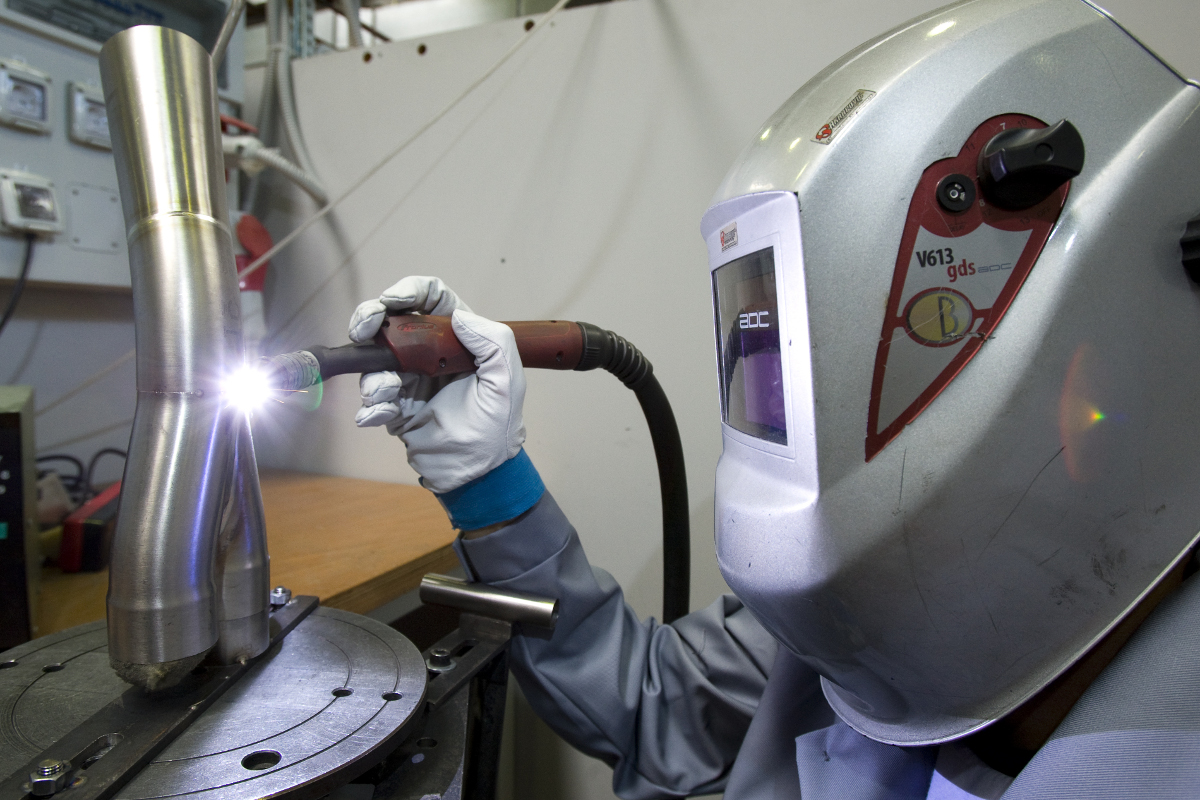
Continuamos aqui a nossa visita virtual às instalações da Akrapovič. Fora das instalações de R & D, partimos para o departamento de construção de protótipos do outro lado do enorme salão, que do exterior parece prateado e moderno. Há um bom número de máquinas especializadas de tornearia entre os vários locais de trabalho fechados. As máquinas CNC brilham numa área separada. Alguns funcionários dedicam-se a serrar tubos, e à perfuração, martelagem e furação de componentes de silenciadores. Faíscas de soldadura iluminam repetidamente o espaço por trás das cortinas de proteção. A atmosfera é agitada. Há claramente vários itens a ser trabalhados ao mesmo tempo, tanto em novos sistemas de escape para produção em série posterior como em sistemas especiais de corrida que são necessários apenas em números pequenos.
É também aqui que as ferramentas e gabaritos necessários são feitos para a produção em série posterior. Não há uma única motocicleta à vista; Há apenas um Audi S7 numa rampa, a receber um sistema de pós-venda. Segundo a Akrapovič, apenas os mais habilidosos artesãos e magos da soldadura trabalham aqui.
No meio do corredor há uma ampla escadaria de aço que leva para cima. No primeiro andar, é a área reservada para o gabinete de Igor Akrapovič. Na frente, num espaço aberto, um punhado de famosas motos de corrida verdes, vermelhas, azuis e laranja. Além disso, dispostos numa fileira de apoios, estão cerca de três dezenas de motores de corrida – todos com escapes “Akra”.
Mono, Twin, três, quatro e cinco cilindros. Monocilíndricos, paralelos, 4 em linha, 4 em V, boxers, todos os tipos de motor. Todas as marcas possíveis, todas as classes de capacidade. Todas as categorias e segmentos, estrada e off-road. Testemunhas silenciosas de uma história na competição já lendária. Esta coleção privada de Akrapovič representa apenas uma parte das máquinas com as quais a empresa trabalhou.
Assim que recuperamos o fôlego de tais preciosidades, saímos do salão e atravessamos o pátio para um prédio separado, onde o trabalho de banco de ensaio é realizado para as motos de estrada. Esta área foi propositadamente separada do departamento de R & D, para não atrapalhar a carga de trabalho consistentemente alta. Os protótipos de sistemas para veículos novos são modificados e testados até que forneçam resultados convincentes em todas as áreas relevantes. Só então passam à produção em série.
O banco de ensaio Superflow está equipado com a mais recente tecnologia de medição para recolher todos os dados necessários. Uma ventoinha gigante dirige o ar de arrefecimento sobre a peça em teste. Uma KTM RC 390 CUP nova foi colocada na plataforma para fins de demonstração. Juntamente com as características do motor, potência e binário, a acústica e as emissões também são registradas e analisadas. Para as várias homologações (E/EG) exigidas para uso em estradas públicas, a empresa coopera com as autoridades alemãs da TÜV, cujos engenheiros de teste participam dos testes necessários no local, onde podem examinar os dados técnicos e aprovar os dados dos sistemas de escape diretamente.
Há também um edifício insonorizado ao lado que tem um banco para carros. Todo o edifício, com outras áreas de trabalho para os veículos, é mantido a uma temperatura constante, fresca e agradável, a fim de proporcionar um ambiente consistente para os resultados dos testes e uma ótima comparabilidade. Mesmo após o final do dia de trabalho, a instalação continua a ser usada de forma significativa. Como o enorme ventilador do sistema de arrefecimento gera uma força impressionante, os competidores de salto em ski desfrutam do uso regular da instalação para os ajudar a treinar. Uma parte importante do salto em ski é manter a postura correta num fluxo de ar forte.
Avante para o próximo prédio. No laboratório interno, dá-se a verificação contínua das ligas de titânio produzidas na fábrica e da sua composição química, a fim de manter os altos padrões em todos os componentes. Os silenciadores completos e os conjuntos de tubos são retirados dos ciclos de produção e são cortados e medidos, as juntas de soldadura são examinadas ao microscópio e /ou submetidas a testes de carga. Não é por nada que o fabrico preciso e a precisão de adaptação imediata dos sistemas eslovenos já são lendários. E essa reputação é mantida com um rigor de ferro.
Uma área separada é reservada à fundição interna de titânio. Certos componentes, como alguns coletores para sistemas de válvulas, configurações de tubos formados em X ou peças ocas complexas, são fabricados num processo de fundição, o que dá vantagens na construção e, além disso, ajuda a economizar peso. A temperatura num forno de titânio chega a atingir os 1.700 °. Mesmo os resíduos de corte do dispendioso material, que anteriormente não tinham utilização, podem agora, graças a processos especiais de reciclagem, ser reutilizados com sucesso.
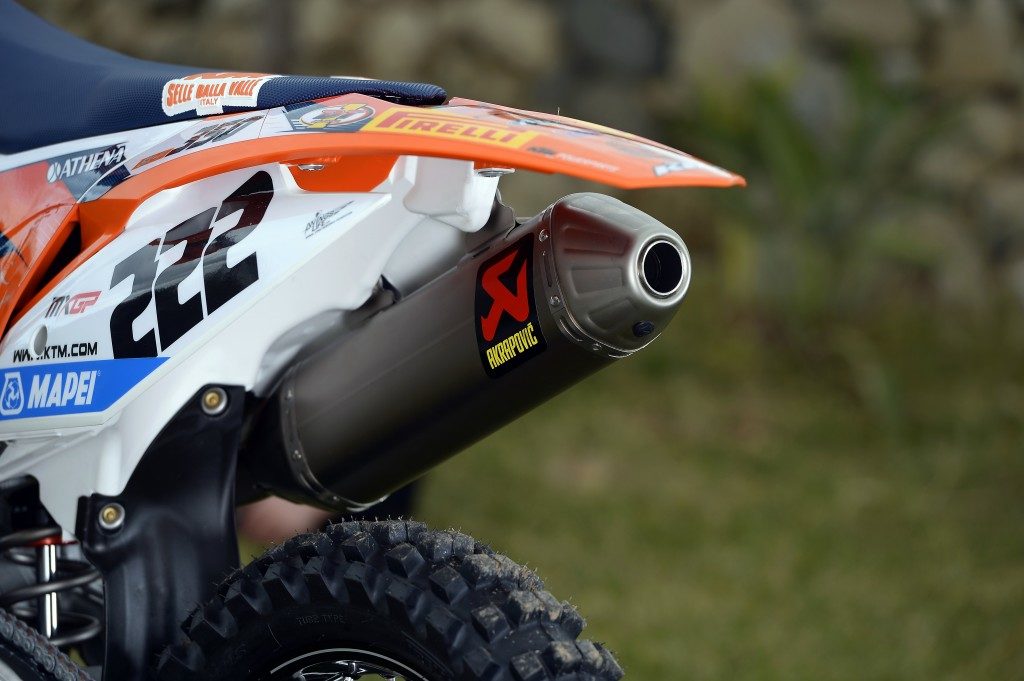
Cairoli é outro a beneficiar da tecnologia Akrapovic
Nenhum outro fabricante de escapes possui tais conhecimentos de trabalhar com titânio. Isso, por sua vez, abriu novas áreas de negócios para a empresa, por exemplo, no setor de tecnologia médica, no qual é necessária uma construção leve e de alta resistência, combinada com uma fabricação precisa.
Quando se trata de produção em série, ela é feita com alta precisão a nível industrial. Tubos de diâmetros variados são dobrados e depois serrados usando máquinas especializadas, o material laminado é prensado, cortado a laser e formado. Formas extremamente complexas podem ser realizadas através do uso de uma máquina especializada de hidro-formação, que opera usando água a uma pressão muito alta. O titânio e o carbono não são os únicos materiais a serem completamente processados internamente; aço inoxidável também é usado até certo ponto. Por exemplo, para sistemas de escape de customs ou scooters de grande capacidade (de 125cc para cima); este grupo alvo também foi servido pela Akrapovič por algum tempo.
Depois de todas as peças necessárias terem sido preparadas, vem a montagem. Muitas peças individuais são juntas usando máquinas automáticas de soldadura, mas a maior parte de todo o trabalho é realizada manualmente. Há um número notavelmente alto de funcionários a trabalhar no departamento de produção. Em inúmeros pontos, encontram-se os soldadores de Akrapovič, homens e mulheres, cada um reunindo cuidadosamente componentes em forma de tubos, placas, suportes e apoios. Na montagem final, todas as partes componentes se reúnem e são rebitadas e completadas usando as peças de fibra de carbono correspondentes. Depois de embalados, os silenciadores de panela e os sistemas completos são enviados para todo o mundo.
Como a procura pelos seus produtos, assim como o número de funcionários, está a aumentar ano após ano, a fábrica está em explosão e todas as medidas de expansão parecem insuficientes. Portanto, apenas uma opção permaneceu: no final de 2004, a produção foi transferida cerca de 100 Km para o sudoeste, para Crnomelj. O local de uma antiga fábrica de compressores oferece quatro vezes mais espaço para a fundição de titânio e toda a fabricação dos sistemas de escape em série. A sede da empresa, no entanto, juntamente com Pesquisa e Desenvolvimento, e o departamento de corrida e fabricação de protótipos permaneceram em Ivancna Gorica.
0 comments